Cost Reduction in Manufacturing Industry
“Costs do not exist to be calculated. Costs exist to be reduced” – Taiichi Ohno
In this age of aggressive competition, manufacturing companies are struggling to improve their bottom lines. Hence it is imperative to achieve cost reduction in key business processes such as production, procurement, inventory, and so on, to ensure and improve profitability.
What is Cost Reduction?
Cost Reduction is the process to identify and remove unnecessary expenses from businesses to increase profits without impacting product quality.
I recently had an opportunity to discuss with a Cost Reduction Consultant, Mr.Ninan Chandy, from DeltaEta Cost Reduction Consultants Pvt Ltd, who is an ardent follower and practitioner of the above-mentioned principle. He has turned around loss-making manufacturing units into highly profitable organizations by implementing successful Cost Reduction strategies and processes.
Here is an interesting example, he shared, that shows how companies incur additional costs unknowingly, which ultimately impacts product price as well as profitability.
A Transmission line tower manufacturing company was regularly losing orders and facing stiff competition inspite of quoting with the lowest possible margins. Upon careful examination, they found that the raw material they required to manufacture a tower was more than their competitors.
On further investigation, it was found that every layer in the designing and marketing process was adding an extra margin of safety. e.g. designers were adding 5% to 10 %, design approver another 5% , manager another 5%. As a result, they were consuming beyond the required level. The problem was in design which when rectified resulted in making the company a leading manufacturer in the region.
So, effective cost reduction efforts should start from design and run all the way to dispatch.
Key Learnings to achieve Cost Reduction in Manufacturing
Let me share with you the key learning from my discussion with Mr. Ninan Chandy to achieve Cost Reduction in Manufacturing.
1. Procurement Policy
Implement a companywide procurement policy to reap the benefits of aggregate demands.
Concentrate on following procurement activities to achieve optimum procurement costs
- Aggregate demand indents from functions, locations, and departments.
- Place bulk orders with staggered delivery to get competitive prices from suppliers
- Increase your supplier base, find local suppliers who can provide quality materials
- Plan logistics well in advance in order to ensure timely deliveries and save costs
- Before buying double-check whether any material is available in stock which can be used without or without modification
With this, companies will be able to negotiate with suppliers, procure goods at optimal costs and lead time resulting in lower costs and inventory. All of these will result in significant cost reduction.
You can also leverage eProcurement software to digitize, automate and make the Procurement process transparent & fair. This will also speed up the Procurement process and achieve the above-mentioned objectives.
2. Focus on the Important Key Performance Indicators
Always focus on important KPIs of your business processes which are direct pointers and raise a flag for increasing costs and timelines. Keep a track of the trends to get valuable feedback and identify areas of cost reduction. You can thus take quick and informed decisions for remedial measures to reduce costs.
Focus on the following KPIs to achieve cost reduction in manufacturing.
- Inventory turns
- Breakeven Values
- Delivery delays due to material storage
- Cost of holding stock
- Supplier performance and more
For E.g. If the value of your STR is continuously increasing, it is a clear indicator of a flaw in the inventory control, procurement process or a fall in the sales and an alert to fix it immediately.
3. Need Audit
Companies need to ask tough questions such as Do we really need this material for our operation? at various levels such as Design, Procurement planning, Inventory control, etc.
For e.g. Many a times companies over design products or over-consume materials to provide an extra margin of safety. This practice does not improve the value of the end product. However, a chain of such actions in operation increases costs by a large margin. Hence, always be watchful on key materials consumption.
Also, you should always be on the lookout for identifying alternate and economic materials which can be used without affecting product quality.
4. Waste Reduction
Some amount of waste is given in any manufacturing process. Wastage may be in the area of material, manpower, energy, time or elsewhere. Manufacturing waste occurs during production, because of defects, in case of excess inventory, while transportation, and so on. Companies should always look for opportunities to eliminate waste. E.g. Reduction in scrap generation during the fabrication process will improve profitability significantly.
5. Develop a culture of Cost Reduction
If we have to define Cost Reduction mathematically, it is the sum total of all the tiny efforts taken consistently over a period of time. Therefore, cost-saving of amount X = X1 + X2 + X3 + X4 + ………. + Xn.
Hence, Cost reduction is not just about a strategy, process or technique. It is a culture that needs to be developed across the company. Each and every employee of the organization must focus on “Money Saved is Money Earned”. Guide, motivate and coach teams to build a long term culture of cost reduction.
Educating your employees, how even a tiny cost reduction, can contribute to improving the profit margin of the company, will ensure that employees appreciate the importance of cost reduction. Rewards & Recognition of employees who follow processes and identify areas of improvement can also motivate others to follow suit.
6. Leverage Technology to achieve Cost Reduction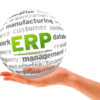
Companies should leverage ERP software to digitize, automate and speed up business processes, increase productivity & efficiency. Centralized information management, improves visibility & information sharing, you achieve better coordination among functions and departments. Specific KPI based reports & insights into business trends help make timely, data-backed and informed decisions. All these effectively help in reduction in manufacturing, administrative, operational costs across the organization.
7. Focus on Saving of Unit Cost and Not Expenses
The ultimate objective is to focus on Savings of Unit cost. Keep a close eye on the manufacturing cost per unit. For e.g., if the manufacturing cost of a critical item is Rs. 10 per unit. With a continued focus on improving processes and eliminating wastages, you may be able to lower the manufacturing cost to Rs. 9 per unit. This means you have reduced manufacturing costs by 10%. The Rs. 1 saved can be seen as net profits, boosting your bottom line dramatically Thus, you will be able to see a significant increase in your profit margins.
8. Implement Cost reduction and Not Cost Cutting
The difference between cost reduction and cost-cutting can be explained vide an example.
To reduce air pressure in an overinflated tyre, we reduce the air inside and not cut the tyre!!
Cost Cutting is a temporary measure to reduce costs while cost reduction is a permanent result.
Cost Cutting is a reaction to decreasing profits while cost reduction is a proactive approach to improve competitiveness.
Actionable Steps to achieve Cost Reduction in Manufacturing
In order to ensure successful cost reduction in manufacturing, companies should:
- Identify the Biggest Costs and mark cost-cutting areas for continuous improvement
- Start cutting costs slowly without affecting the quality & efficiency
- Eliminate redundant activities/purchases that incur significant costs
Summary
The most important benefit of cost reduction in manufacturing is that you can lower your product costs and boost your profits. You can set competitive prices of products & gain an edge over competitors.
So, look all around you to cut every little bit from your costs. Remember cost reduction is not achieved in a single day or by doing a single activity. It is the sum total of all the tiny efforts taken consistently over a period of time.